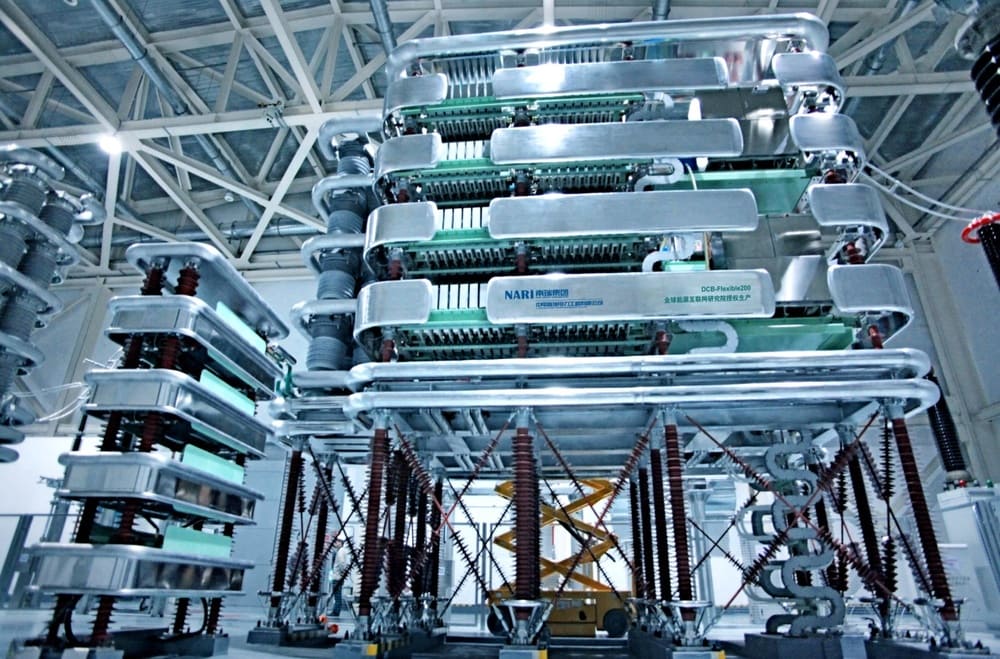
Photo from NARI company website just for show (world’s first set of 200kV DC circuit breaker) by C-EPRI company
General about switching condition for HVAC & HVDC grids:
Switching has been the prime technology to control the safe flow of power.
In traditional AC systems, a large number of switchgear can be identified for a myriad of different functions. The most critical switching device is the circuit breaker; a device that can switch on and interrupt fault and normal currents during a short-circuit in a system.
Its function is to isolate faulted sections of the power system in a short time so that power flow in the healthy parts of the system remains unaffected. In a traditional point-to-point HVDC transmission system, however, there is no need for such a dedicated fault current interruption device.
Normally, a fault in such a system automatically leads to a total loss of power in the affected pole line. Fault current in such systems can be cleared by converter control actions at either end or by AC circuit breakers at the AC side.
Almost all of the HVDC systems in operation in the world are point-to-point systems:
A single HVDC link connecting two HVDC stations nearby large-scale generation, e.g. a large hydropower plant and a large load center. With the need of connecting huge amounts of large-sized generators (commonly renewable sources) spread across a large surface, meshed HVDC grids or multi-terminal HVDC systems are being realized on a small scale and conceived on a large scale, aimed to harvest hundreds of gigawatts in a few decades from now. The meshed or multi-terminal topology greatly enhances reliability, system stability, and electricity trade.
A key requirement of such meshed HVDC grids is the possibility to de-energize faulted parts and/or branches of the grid (submarine cables in an offshore grid) without endangering the integrity of the system as a whole.
Faults are inevitable. In submarine cable links they occur at a frequency in the order of 3 faults per 1000
km/year in HVAC applications and 0.2 – 2.0 per 1000 km/year in HVDC projects.
For more information about HVDC switching challenges please read this post on the switchgear content website.
During system restoration, there is no or limited energy flow. Especially in systems having submarine connections, repair times can be very long.
The HVDC circuit breaker is a good candidate to interrupt any possible fault current and isolate the faulted section from the grid in a very short time in order to maintain system integrity.
Other options of HVDC grid protection include the use of converters having fault-blocking capability (full-bridge topology). In this case, the grid de-energizes shortly, and fault current is reduced to levels allowing separation of the faulted section under near-zero voltage and current conditions. This requires fast mechanical disconnectors to be installed at the ends of each DC line.
The DC side circuit must completely de-energize before these fast disconnecting switches are operated.
Anyhow, costs of protection will be rather high: the investments for system protection (including HVDC circuit breakers) for HVDC grids are estimated up to 9% of the total project costs.
Compared to HVAC fault current interruption HVDC fault current interruption is challenging because of the following 3 reasons :
1-Absence of zero points in HVDC circuit breakers:
There is no natural current zero in DC systems unlike in AC systems. This implies that there is no moment when the inherent magnetic energy (½Li 2 ) in the system is zero. For AC current interruption, current zero provides the opportunity to interrupt at the moment when there is no magnetic energy in the system.
Thus, the AC circuit breaker does not need to absorb magnetic energy in the system whereas the DC circuit breaker must have a provision to absorb several Megajoules of the energy in the (faulted part of the) system.
For example, the magnetic energy stored in a 100 km faulted line carrying 15 kA of current is around 11 MJ. Converted into mechanical terms, this is equivalent to the kinetic energy of a 30-ton truck running at 100 km/h, which has to be stopped in a matter of a few milliseconds. Whereas a buffer would be designed to bring the truck to a standstill, a sustained counter voltage generated by the DC circuit breaker has to counteract the DC fault current and must bring the fault current, to a “standstill”.
2-Need a quick reaction for the HVDC circuit breaker than HVAC circuit breaker:
The peak value of fault current in DC systems is limited only by the resistance (R) in the current path, whereas in AC systems it is the inductance (L) of the conductors that limits the fault current. In power systems, R << ωL (standardized value of ωL/R = 14 – 17). This implies that, provided the DC source is strong enough, very high prospective DC fault currents can emerge, see Figure 1. Therefore, HVDC breakers need to act fast, around ten times faster than AC breakers to clear a fault current on its rising edge before reaching its peak value. With rate-of-rise of fault current (di/dt) in the range of a few to several kA/ms, breaker operation time may not exceed 8 – 10 ms in order to handle technically feasible values of peak fault current (Ipk). Though this current is much lower than the rated short-circuit breaking current of AC breakers (63 -80 kA), the challenge in DC current interruption is in realizing a short breaker operation time in order to limit undesirable consequences for system and converter. In addition, the rapid response also calls for the need for very fast DC fault protection. Values in the range of 1 – 3 ms of relay time (tRY) are reported as feasible.
Figure 1: fault current interruption curves in HVDC (left) & HVAC (right)
Photo from D10.9: Reporting on HVDC circuit breaker testing PROMOTioN – Progress on Meshed HVDC Offshore Transmission Networks document chapter 2
3-Ability to withstand for TRV than AC circuit breaker:
To interrupt fault current, HVDC circuit breakers need to quickly generate and sustain counter voltage exceeding the system voltage. This voltage is henceforth termed as Transient Interruption Voltage (TIV) see Figure 1 whereas there is no such need for an AC current interruption. Rather an AC circuit breaker needs to sustain a system imposed transient recovery voltage (TRV) imposed by the system.
HVDC circuit breaker testing:
The different challenges of both types of circuit breakers have an impact on testing. Testing of HVDC circuit breakers is fundamentally different from that of AC circuit breakers as both voltage across and current through the circuit breaker exists at the same time during the energy absorption phase, leading to an energy absorption requirement.
You can find the article about the HVDC circuit breaker Synthetic Current Test here.
Before commissioning HVDC circuit breakers in practical applications, adequate verification of its ratings and functionality through testing is crucial. Meaningful demonstration of HVDC circuit breaker technology is achieved when the applied tests accurately reflect realistic fault conditions, e.g. in multi-terminal HVDC networks. Hence, to accelerate the realization of the envisaged MTDC networks, test facilities sufficiently representing a practical DC system under various conditions are designed and developed.
In standardization, so far there are no internationally accepted specified and quantified test requirements of HVDC circuit breakers let alone a standardized method to test these devices.
In the project, a test program is agreed among the participating manufacturers on a test program covering the main duty of HVDC circuit breakers: breaking of current up to its rated peak fault current.
Most of the content of this article is taken from the article: D10.9 Reporting on HVDC circuit breaker testing PROMOTioN – Progress on Meshed HVDC Offshore Transmission Networks by KEMA Labs: René Smeets, Nadew Belda , MEU:Hiroki Ito, Takashi Inagaki , SciBreak : Simon Nee , ABB: Semere Mebrahtu-Melake , DNV GL :Cornelis Plet