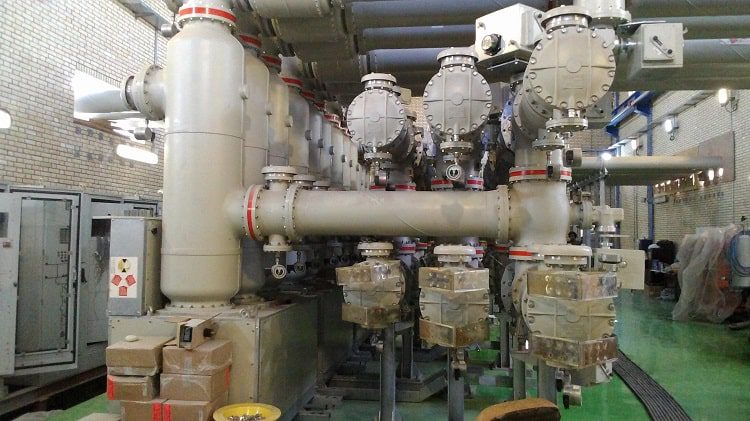
The data management for spare parts of gas-insulated switchgear (GIS) will give an overview of information related to the specifics of the installation. It provides a view of what information could be important in case of maintenance, repair, or upcoming failures.
Data management of gas insulated switchgear (GIS):
Data management begins with the manufacturing and routine testing of the gas-insulated switchgear (GIS) in the factory; it collects information during erection and commission tests and operation time. The data management is the basis for evaluation of the condition assessment of the GIS. It shows the history of the GIS and allows predictions about the upcoming operations.
Decisions about maintenance, repair, or replacement strategies are using the collected data of the GIS.
In the following, some aspects are presented on information, strategy, and evaluations based on data management are given.
Spare parts availability of manufacturer obsoleted design in gas insulated switchgear (GIS):
The availability of spare parts is important for the service of the GIS. Not available spare parts of obsoleted design need to be manufactured as a single pieces which could be very costly.
GIS installations have been in operation for decades. The first GIS system installed in 1968 is still in operation. The availability aspect of spare parts needs to be seen under the aspect that the type of GIS in operation is no longer manufactured or even the manufacturer of the GIS is no longer in business.
Not all types of spare parts are recommended to keep in storage for such a long time. O- rings or cast resin insulators may change their physical structure and may not be usable after 20 or 30 years. Mechanical parts may be reproducible in case the original production drawings are available, but at a high cost.
Most changes are related to the secondary system which usually shows lifetimes of less than 10 years. It might be a better way to replace the secondary system instead of storing spare parts.
The condition of the primary part of the gas-insulated switchgear (GIS) is much dependent on the network requirements of power transmission levels or a number of switching operations. Because of the high-cost GIS functional units, it is not recommended to store complete, gas-filled GIS units in the case of replacement.
These GIS functional units need to be maintained as the GIS itself, which causes additional costs. The spare part aspect is complex and needs to be discussed and decided in agreement between the user and manufacturer. This agreement may change over time with technology and management changes of the user and manufacturer. Time-based maintenance is more and more replaced by condition-based Maintenance or no-maintenance with early replacement of gas-insulated switchgear (GIS).
Spare part handling and storage are costly and difficult to plan. Besides the material of the spare parts, it is also necessary to have skilled workers to carry out the replacement of GIS parts.
This requires the availability of special tools, which may not be available anymore. The older the gas-insulated switchgear (GIS), the more serious are these aspects.
It is like an old clock:
It’s nice to have it on the wall, but for repair, a specialist needs available who understand the technology, can reproduce parts, and assemble these with special tools. If this is economic or not depends on the view of the owner.
Age of gas insulated switchgear (GIS) components:
The age of components can indicate the quality and expected remaining lifetime of the GIS. The impact of aging is very different for the components used in GIS.
Gas-insulated systems, such as GIS, do not show an aging effect when operated within the defined technical limitations of voltage and temperature. This reflects the design of electrical insulation capability of the insulators at the required gas density, low moisture content, and free of particles.
Cast resin insulators within the GIS are operating far below their maximum electrical field strength. The maximum electric field strength of the cast resin insulator is about the factor 3–4× higher than in gas. For this reason, no electric aging of the insulation is expected.
The operation temperature of the gas-insulated switchgear (GIS) allows maximum temperatures up to 120 °C given to the material limitations of silver-plated contacts and the cast resin of the insulators. The type-tested maximum temperature for the GIS current rating is usually between 80 °C and 90 °C. This means, that in the case of operating the GIS in its given limit of ambient temperature and rated current no thermal aging can be expected.
The more than 50 years of experience with gas-insulated switchgear (GIS) installed and in service reflects these physical features of gas-insulated systems. In the case of dielectric failures, they typically occur at the beginning of operation usually within the first year. In most cases, the reason for these failures is in the assembly process on site or with quality problems during production. When GIS is in operation under normal conditions, usually no dielectric failures are reported.
Metallic enclosures made of cast aluminum are designed as pressurized compartments with a safety margin of factor 2.6 according to standards and do not show any aging effect.
The aging effect is mostly related to secondary equipment and mechanical drives of switches and circuit breakers. CIGRE investigations have shown that failures in GIS are linked to failing motors, mechanical relays, electronic switches, loose cables, contacts, or contact corrosion.
The reasons for these failures are linked to corrosion, overload conditions with too much heat, the impact of pollution with moisture and dirt, mechanical stress from the surrounding area with vibrations of machines, traffic, or railroad, and impact from resonances in the building or structure.
To get an overview of the age of the different parts of the gas-insulated switchgear (GIS) installation, the year of erection and replacement or repair should be listed.
High voltage gas insulated switchgear from XIAN-XD company
Identification of critical parts for gas insulated switchgear (GIS):
The identification of critical parts will help to be prepared for a failure and the availability of the failed part.
Critical parts of gas-insulated switchgear (GIS) are depending on the importance of their function in the network. Connecting a large power plant to the network for delivery of baseload energy has a higher power delivery requirement than a remote housing area of low load concentration.
The scheme of the GIS installation at these substations shall reflect the importance of power delivery.
In low-level availability, a single bus bar scheme will provide an adequate Power supply, while for high-level availability, double or triple bus bar schemes or breaker and half schemes are used to provide more flexibility in cases of failure and provide a high level of power supply.
To choose the right substation scheme for the gas-insulated switchgear (GIS), the first step is to avoid power interruptions.
Critical parts of GIS can be bypassed by redundancy in the substation scheme And isolate the critical part of the gas-insulated switchgear (GIS) bay for repaired.
To identify critical parts of GIS that are specific to the manufacturer’s design and may be identified by the manufacturer’s experiences and data collected from gas-insulated switchgear (GIS) in operation.
For the measures coming from identified critical parts in a GIS substation, a Concept of provision, storage, replacement, and repair needs to be agreed upon with the manufacturer.
For the identification of critical parts in substation design, it is recommended to evaluate the importance and scheme of the substation. The need for gas-insulated switchgear (GIS) units and parts to be stored or produced at the factory on demand is recommended to discuss and agree upon with the manufacturer.
I am looking High voltage link
Please connect me on LinkedIn.