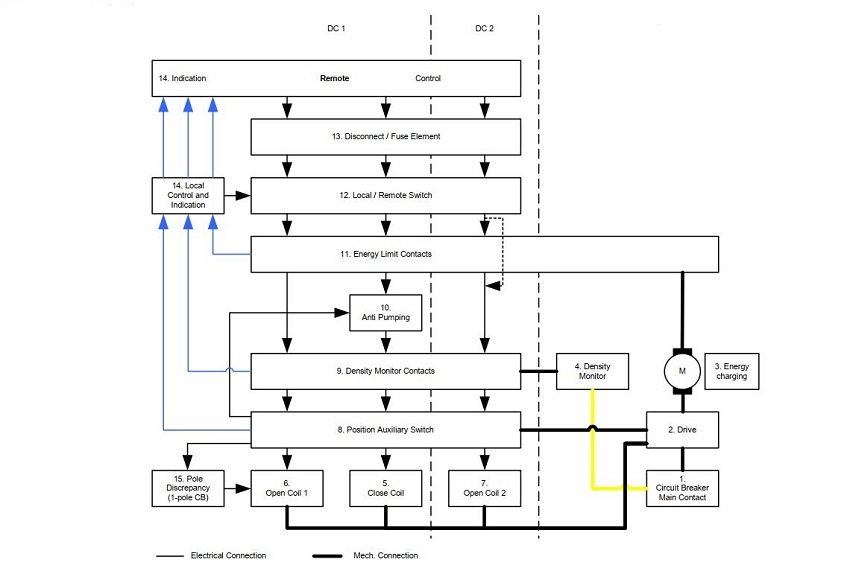
Photo from CIGRE NO 319 Brochure
Circuit breakers control circuit functions diagram description:
1:Circuit breaker Main Contacts (not part of the control circuit).
2:Mechanical operating mechanism that releases the energy to move the main contacts((open and close)(not part of the control circuit).
3:Energy charging system: provide energy to the operating mechanism.In the case of hydraulic, spring, or
pneumatic energy storage systems, this is an electric motor or a motor operated pump or compressor.
4&9: Density monitor and density monitor contacts: These devices provide the means for supervision of the insulation and/or arc extinguishing media; typically SF6 or mixed gas in modern circuit breakers. Temperature compensated pressure switches are commonly used which operate auxiliary relays to prevent
the tripping or closing of the circuit breaker if the SF6 gas density in the enclosure falls below critical levels. There are two functions that are performed by these switches and contacts:
- To provide a warning or alarm in case of reduced SF6 gas density in the enclosure before the lockout level is reached. This is an alarm only and provides time for the operator to correct the problem before the circuit
breaker locks out and loses functionality. - To interlock or prohibit operation of the circuit breaker when the SF6 gas density reaches a level (“lockout level”) where it will not operate safely.
Typically the operator has the option of requiring the circuit breaker to automatically trip and lockout when this level is reached (“forced trip”) or having the circuit breaker lockout in the current position. The former option
carries some safety risks.
5:Close coil: These are solenoid devices which are energized in the event of a valid closing signal being received by the circuit breaker. Energization releases the mechanism thereby closing the main contacts of the circuit breaker. Once the circuit breaker reaches the closed position, auxiliary switch contacts in the closing circuit open and de-energize the closing coils. Typically, there is only one closing coil in the control circuit.
6&7:Open coils: These are solenoid devices which are energized in the event of a valid opening signal being received by the circuit-breaker. Energization releases the mechanism thereby opening the main contacts of the circuit breaker. Once the circuit breaker reaches the open position, auxiliary switch contacts in the trip coil circuits open and de-energize the trip coils. There are typically two trip coils that operate from independent power supplies. The operation of only one trip coil is sufficient to operate the circuit breaker. Two coils are provided in order to minimize the risk of a failure to trip.
8: Position auxiliary switch: These contacts, which are driven by the operation of the circuit breaker, are used to interrupt the current of the close and trip coils to de-energize them when the operation is complete. They are also used for indication and monitoring of the circuit breaker position and to interlock control & protection operations at the bay or station level to prevent an incorrect switching operation. These switches can be used for any function where the position of the circuit breaker is a required parameter.
10:Anti-Pumping: Anti pumping refers to the prevention of a re-closing operation in the situation where a previous close command is still applied to a circuit breaker that has been opened. This prevents the circuit breaker from
repeatedly closing and opening. Typically the close command energizes an anti-pumping relay via an auxiliary switch contact (a Normally Open (NO) contact). One contact of the anti-pumping relay interrupts the circuit to the close coil. A second contact is used to latch or “seal in” the anti-pumping relay until the close command is removed from the circuit.
11: Energy limit contact: The energy limit contacts are set to operate when the stored energy in the mechanism is depleted either by operation or losses. Typically they start a motor in order to restore the energy of the mechanism to its normal operating level e.g. spring position, hydraulic/pneumatic pressure.
For spring mechanisms recharging is typically after every close operation whilst other mechanism types may be able to perform several operations before recharging is required. Pneumatic & hydraulic systems have a switch which monitors the pressure and energizes a compressor when it falls below a critical level. When the energy level is restored, a switch opens, which stops the motor.
The motor typically has protection against thermal overload and a time limit relay, which will stop the motor (or a motor operated pump or compressor) in the event of a malfunction. The switches or contacts monitoring the stored energy, therefore, perform the following functions:
• Lock out the close operation if the circuit breaker does not have enough energy to close and re-open safely.
• Lock out the open operation if the circuit breaker does not have enough energy to open safely. This is typical for hydraulic or pneumatic circuit breakers but not for spring operation where a successful closing charges
the opening spring(s).
• Control (start and stop) the charging circuit of the energy storage device (e.g. spring).
12:Local/remote switch: This is a selector switch which allows the operator to interrupt remote control and only operate the circuit breaker locally. This is a safety feature to prevent remote operation of the circuit breaker while it is being serviced.
13. Disconnect/Fuse element: These devices are used to interrupt the power to the control system during maintenance work or during a fault to the control circuit. Disconnection is typically provided by knife switches or removable fuses/links which provide visual confirmation that the control circuit is open and which may be locked open to prevent unauthorized re-instatement. Where protection against short circuit is required, Mini Circuit Breakers (MCB) may be used as an alternative to simple fuses.
14. Local control and indication: This function provides an indication of the position of the circuit breaker and the status of the local/remote control facility.
These indicators are for maintenance or emergency operations (depending on local safety rules).
15. Pole discrepancy/pole disagreement circuit: For Independent Pole Operation (IPO) circuit breakers (one mechanism for each phase); it is possible for one phase of the circuit breaker to not have the same position (open or close) as the other phases. This situation is called pole discrepancy or pole disagreement and can result in an unsymmetrical primary current. Auxiliary switch contacts in each phase are used to energize a time delay relay in the event that a pole discrepancy occurs. Assuming the discrepancy condition is persistent, after the preset time delay, an attempt will be made to trip all phases of the circuit breaker. In the event that the pole discrepancy was due to a failure to close of one pole, this trip is likely to succeed. However, if the initial discrepancy was due to a failure to open, the failed pole is unlikely to respond to subsequent opening commands and opening of other circuit breakers may be necessary. The preset time delay is normally between 1.5 to 5 seconds. The time depends on the specific grid conditions and how long the primary circuit could have operated asymmetrically (should be longer than 1 phase auto reclose time and shorter than the negative phase sequence protection of generation).
16. Heating: Space heaters are often provided in each of the operating mechanism and control housings to reduce condensation.