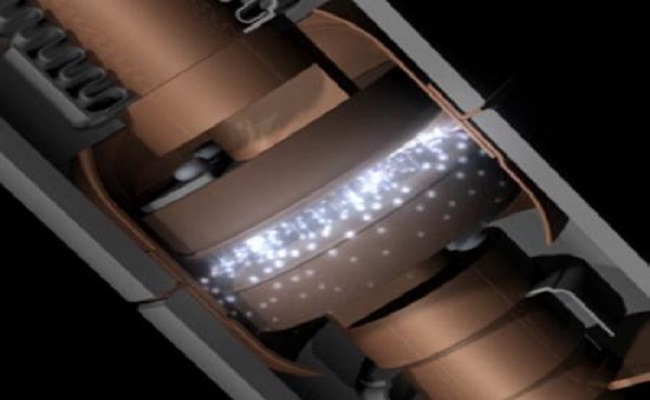
A vacuum interrupter, based on elastic damping elements made of refractory metals and impregnated with a fusible eutectic, can be used in vacuum switching apparatus, especially in systems requiring the switching of large currents (e.g., electrolyzers for hydrogen and metal production) or high-speed switching (e.g., medium voltage direct current).
They are also suitable for instantly increasing the switching capacity of existing systems (e.g., safe boosting of OLTC for wind turbine transformers).
Using elastic contacts removes the limitations on the nominal current magnitude caused by the quadratic increase in compression forces. Additionally, new systems can be smaller and cheaper. Further research and inclusion in standards based on these studies are necessary for implementation.
Concept of Elastic Contacts in Vacuum Interrupter:
In their essence and mechanics, elastic contacts for vacuum interrupters are typical wire mesh vibration dampers (Fig.1) made of refractory metals, impregnated with low-melting alloys that provide contact through the liquid phase.
In early literature, the term composite liquid-metal contacts is used, but this is not a defining characteristic of this specific type of contact, as the liquid phase exists as a thin layer on the surface of the refractory wire.
In contrast, the important characteristics, namely anti-vibration and contact over the entire visible area, are achieved thanks to the properties of the knitted damper.
Figure 1: Elastic Contacts
That is why these elastic contacts do not have an inertial rebound, cannot weld, do not have, in the usual sense of the word, contact resistance, and, as will be shown later, do not experience electromagnetic separation.
But if these contact materials have such outstanding properties, why are they not yet widely used in electrical engineering?
Main Problems `of Elastic Contact Materials in Vacuum Interrupter:
1. Production Technology: Until now, the technology for manufacturing and applying elastic contact materials required very expensive equipment, complex thermochemical processes in a hydrogen atmosphere, and, accordingly, specially trained personnel. The problem is that Gallium and its alloys have poor adhesion to tungsten and other refractory metals.
2. Lack of Consolidated Information: Existing information on research into such elastic contacts has not been consolidated into one source and is not well-known to specialists.
3. Lack of Systematic Research: Systematic studies that would allow engineers to apply such materials have not been conducted so far, despite the outstanding properties of elastic contacts.
Manufacturing Elastic Contacts for Vacuum Interrupter:
The first problem, the technological one, was solved by the author in April 2024, who developed a simple method for the manufacture and application of elastic contact materials (patent application PCTIB2024/054125). The proposed method of manufacturing and applying elastic contacts is simpler and, in most cases, more economical than the manufacture and application of traditional rigid contacts in vacuum switching equipment.
Manufacturing elastic contacts boils down to a few simple operations:
1. Making the Damper: A damper is made from knitted wire, usually tungsten, the same wire that was recently used for incandescent lamp filaments, or stainless steel, in special cases – molybdenum, niobium, rhenium, and their alloys. The technology is widely used to manufacture knitted dampers, as noted, vacuum chamber manufacturers receive ready-made dampers from manufacturers.
2. Soldering the Dampers: These dampers are soldered to the conductors in the same way as rigid contacts.
3. Impregnation with Low-Melting Alloy: Dampers are impregnated with a low-melting alloy, which remains liquid under operating conditions. These are usually various eutectic alloys of gallium, indium, and tin with the addition of alloying elements, such as silver, to lower the melting point.
Switching Tests of Elastic Contacts for Vacuum Interrupter:
Switching tests of elastic contacts in a vacuum interrupter (Fig.2) for durability were conducted in a pre-production vacuum contactor specially designed to work with elastic contacts. During the tests, 200,000 switching cycles at 250A in AC4 mode, current 600 amperes, and voltage 690 volts were completed.
Switching tests for overvoltages showed that overvoltages were 2-3 times lower than the norm.
Figure 2: Switching tests of elastic contacts
FAQ about elastic contact in vacuum interrupter:
QUESTION: What contact pressure is required for your contacts?
Answer: The contact pressure is proportional to the area of the contact material. For a nominal
current of up to 6000 amperes, the contact pressure does not exceed 150 Newtons.
(At this point, it’s important to watch their facial expressions, as they may show doubt, similar to
how psychiatrists observe their patients.)
QUESTION: How do you overcome the electrodynamic blow-off and inertial rebound?
Answer: We don’t overcome the electrodynamic blow-off or inertial rebound. We don’t pay
attention to them at all. (Pause…) Our value for electrodynamic blow-off is 70 times lower. Why?
Because… physics. Simply technical physics of electrical contacts.
The force of electrodynamic blow-off depends on the square of the current and the natural logarithm
of the ratio of the visible contact area to the actual contact area.
QUESTION: How are elastic contacts constructed?
Answer: Elastic contacts in a vacuum interrupter are essentially damping elements made from knitted wire mesh, which are commonly used for damping and vibration reduction. Therefore, no vibrations can occur in our
contacts, meaning there can be no inertial rebound.
With minimal compression, these damping elements fit tightly across the entire visible contact
surface.
Naturally, to be used as contacts in vacuum circuit breakers, they must be manufactured in a specific
way. First, from tungsten, rhenium, molybdenum, or niobium. Second, these high-melting-point
metals must be coated with a low-melting alloy so that the low-melting alloy is securely held within
the wire mesh and ensures conductivity across the entire contact volume and surface.
When elastic contacts close, the connection is made across the entire surface, and the electric current
flows through the liquid phase, there is no reduction in cross-sectional area, no “current bridges,”
and consequently, no electrodynamic blow-off, whether during closing or under short-circuit
conditions.
QUESTION: Quality and stability guarantees: What guarantees can you provide
regarding the stability and durability of your elastic contacts during long-term use? How
does your technology perform under extreme conditions such as high temperatures, frequent
switching cycles, or electromagnetic pulses?
Answer 1: I have a vacuum circuit breaker with elastic contacts that is 17 years old. We can open it
and check the condition of the contacts and whether any intermetallic compounds have formed in
critical amounts.
Answer 2: Elastic contacts can operate in any spatial orientation, withstand accelerations up to 10G,
and the gallium alloy will not leak from the framework. The temperature conditions are limited by
the material of the conductors and the solder used to assemble the vacuum circuit breaker. The tests
were conducted in a mode of 1200 on-off cycles per hour. Regarding EMI, these contacts can even
be used for generating EMI, as no contact vibrations occur.
Most of this content is written from the articles and files sent by Mr. Mykhailo Prytula.
We hope that by publishing this content, the new generation of vacuum breakers with elastic contacts will be used more in the electrical industry.
Thank you, Mr. Mykhailo Prytula for providing the information.