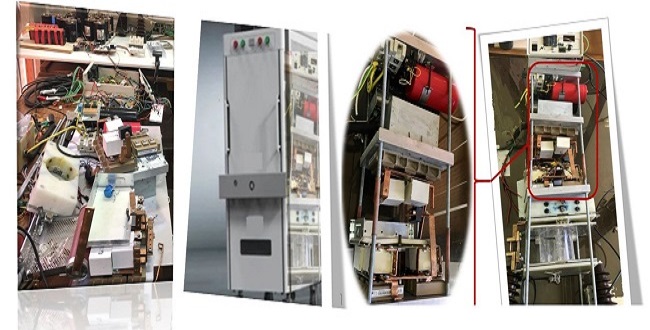
Medium voltage DC circuit breakers are suitable for applications in ships, urban subways, electric trains, microgrids (electric vehicles), distributed generation (solar energy), and battery-based systems (data centers).
The relatively low circuit impedance in a DC case leads to higher amplitudes of short circuits. Furthermore, because transformer windings do not contribute to the overall time constant in DC systems, the overall time constant shrinks and a short circuit can have rise times as brief as a few milliseconds. Voltage collapse may also happen where maintaining at least 80% of the nominal DC voltage is a precondition for the voltage source converter (VSC) station to work normally.
To minimize converter operating disruptions, the fault must be cleared within a few milliseconds, especially for stations not linked to the faulty line or cable.
Medium voltage DC circuit breakers types in the market:
Three main types of circuit breakers in the LVDC and MVDC markets are solid-state circuit breakers (SSCBs), mechanical circuit breakers (MCBs), and hybrid circuit breakers (HCBs) which is a mix of SSCB in parallel with an ultra-fast mechanical switch (UFMS).
Conventional air and SF6-based LV and MV AC MCBs have a certain DC interrupting capability limited to only a few kilovolts and a few Ampers.
Solid-state medium voltage DC circuit breakers:
Topologies for SSCBs are typically based on a certain number of Integrated Gate Commutated Thyristors (IGCTs), Gate Turn-Off Thyristors (GTOs), or Insulated Gate Bipolar Transistors (IGBTs), connected in series. Although the response times are incredibly quick, one drawback is the substantial on-state losses typically in the range of 15-30% of the losses of a VSC station.
The high component costs, lack of galvanic isolation, and inadequate thermal absorption capacity are other disadvantages.
Figure 1 shows some type of solid-state medium voltage DC circuit breaker design:
Figure 1: a) IGCT-based medium voltage bi-directional solid-state circuit breaker, (b) IGCT-based medium voltage bi-directional solid-state circuit breaker, (c) GTO-based bidirectional solid-state circuit breaker
Different SSCB topologies have been proposed. However, most of them are for voltages ≤ 1 kV, in particular for low currents ≤ 1000 A. It should be noted that one of the most challenging aspects of SSCB technology is high on-state loss and, although some articles report an MV SSCB satisfying an MV voltage level such as of 6-15 kV, they are typically for rated current less than 1000 A, But required power handling capacity would be in some MWs to a few tens of MWs range with at least 3 parallel modules (3P:3*3.72 MW).
Thus, developing a DC CB with a rated power of less than 10 MW for future MVDC architectures becomes almost useless. The current power semiconductor technologies cannot meet such power ratings; consequently, SSCBs for the future MVDC architectures will not lead to a highly efficient cost-effective compact design. In this regard, relatively large air blowers with capacities around six thousand cubic feet per minute and/or active water cooling are needed for the multi-kilowatt levels of on-state loss anticipated for high currents.
Hybrid medium voltage DC circuit breakers (HCBs):
Hybrid medium voltage DC circuit breakers include a current conduction path and a current interruption path.
A hybrid breaker combines the exceptionally low forward losses of a pure ultrafast switch with the quick performance of a solid-state breaker in the parallel path. The main breaker is positioned on a parallel path and is made up of a series and parallel solid-state switches that are connected in series.
A developed a modular HCBand one module as shown in Fig. 2 with rated voltage and current, and a current breaking capability of 6.2 kV, and 600 A, respectively.
It’s worth noting that the ultrafast switch’s arc chamber simply needs to generate enough voltage to communicate the current and facilitate the paralleling philosophy of the modules. In all SSCB and HCB designs, a residual current disconnector (RCD) and a shunt resistor to measure the current shown in Fig. 2 is needed. When the current dumps to a low value specified by the leakage current of the metal oxide varistor (MOV), the disconnector opens, isolating the system and preventing any leakage current through the semiconductors and MOV.
Fig 2: Hybrid medium voltage DC circuit breaker
The main path’s UFMS just needs to generate a high enough voltage to commutate the current to the parallel full IGBT breaker. The resistance of the auxiliary DC breaker, Rdson at 2 kA, and the fast mechanical switch need to be less than 20 mW to have similar characteristics as an electromechanical circuit breaker. Utilizing UFMS in the main path results in lower on-state losses and forward voltage than a full SSCB.
The proposed design can be beneficial over the high voltage HCBs manufactured by ABB and Alstom, because (1) there is no on-state semiconductor loss, (2) its control circuit will be simpler, and (3) the expensive “Power Electronic Switch” in the main path, can be avoided. Indeed, only one UFMS can substitute both the “Power Electronic Switch”, and the fast disconnector proposed by ABB for the main path.
However, it needs to ensure that UFMS contact resistance is no more than equivalent electromechanical contacts and has the withstand holding force capability of 4.45×10-7 I2 N (i.e > 178 N for 10x in-rush at 2 kA rated with safety factor 2x or 356 N).
Ultrafast Mechanical Switch in medium voltage hybrid DC circuit breaker:
The challenges for realizing the mentioned philosophy are (1) whether such ultrafast switches can be developed for MV levels, (2) whether the buildup of the arc voltage for commutation is sufficiently high, and (3) whether the same design is possible for RCB. The answer may be YES for all questions as discussed below.
Electromagnetic Thomson coil (TC) actuators operating based on attractive or repulsive forces between current-carrying conductors are very suitable for fast switching because they can achieve high accelerations through precise control. So far, two techniques based on TC have been proposed and well-elaborated for ultra-fast mechanical switches, where the one with series coils outperformed the one based on induction in terms of efficiency. These two techniques were also compared by Multiphysics finite element modeling.
A single phase 12 kV (nominal voltage) and 2 kA (nominal current) / 20 kA (short circuit) fault-current limiting circuit breaker (FCLCB) and 24 kV, 3 kA / 40 kA FCLCB enabling the arc to be extinguished without any forced arc cooling within 100-300 μs were designed, built.
The induction-based fast switch with a rated current of 7 kA accelerates an HCB contact of ~2 kg with an initial acceleration of ~44,900 m/s2 that results in 4 mm contact separation after ~422 μs, enough to withstand a rated switch voltage of 3 kV .
This fast motion should be damped at the end of travel to prevent over-travel, bounce, fatigue, and other undesirable effects.
We express our gratitude for the collaboration of Dr. Ali Kadivar in allowing us to publish this content, which has been largely sourced from their article titled ” Hybrid Ultrafast Mechanical and Solid-State Medium Voltage DC Circuit Breakers: Identifying Ratings, Types, and Future Needs”.